Reactive, scattered planning
Food & Beverage Supply Chain Consultants
Growth-Minded Consulting for Margin-Minded Brands.
We help food and beverage brands unlock hidden margin, optimize operations, and scale with confidence.
Value Chain Advisors
JGardner partners with ambitious food and beverage manufacturers and consumer brands to transform their value chains. We help you cut through the friction, strengthen your margins, and build lasting momentum, so you can
grow wisely
and
win fairly.

What's holding your business back?
Sometimes fast-growing businesses hit a wall. You know there's more potential, but you're too deep in the day-to-day to chase it. You need an experienced partner to help you realize it.
Operators turned advisors.
We’ve been in your seat. Now, we’re on your side. Our team of real-world, C-level experts finds what’s missing, accelerates what’s working, and drives results immediately. Here’s how we help:
It’s not just a proven process for how we operate. It’s a commitment to our clients that says we are here to help you regain clarity, recover lost margin, and grow with confidence.
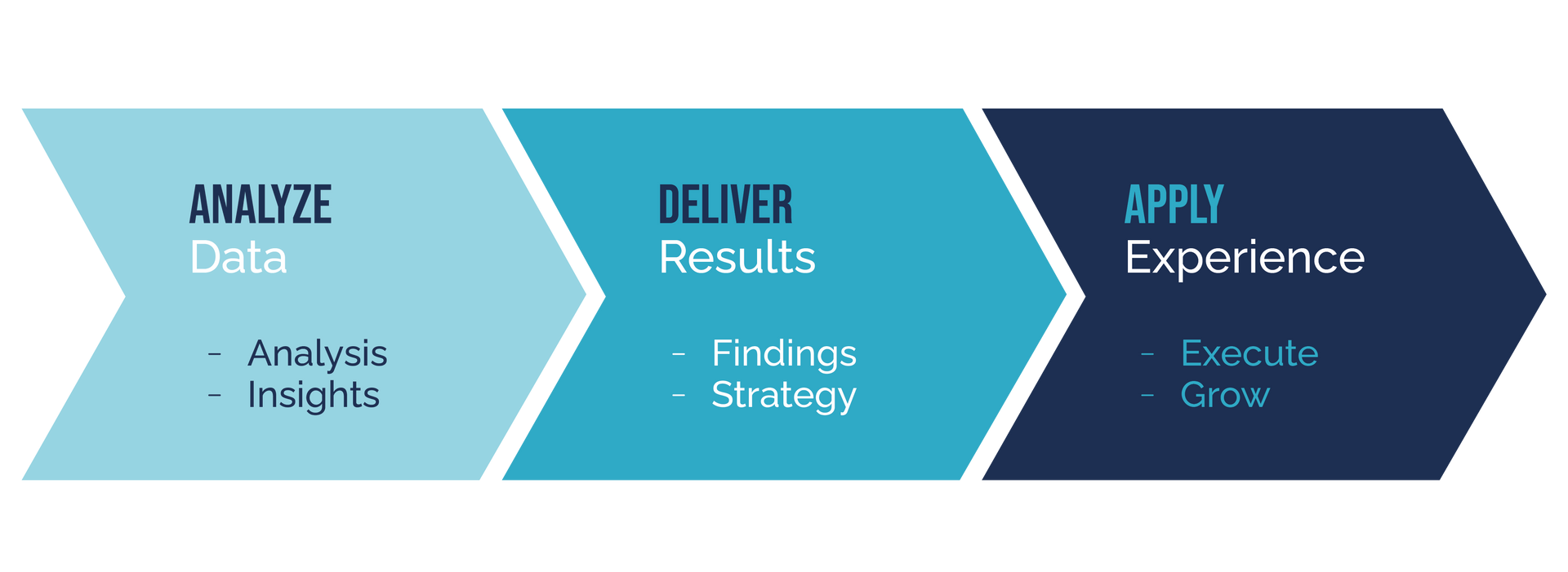
Their success is our success.
Here are just a few of the ways we’ve helped our clients grow wisely and win fairly.
5,191
Agreements Negotiated
$3 Billion
Total Cost Savings
$100 Million
Largest All-Time Single Savings
$80 Million
Largest Savings in
Food + Beverage
From The Blog
Insights Worth Your Time
Explore short, sharp insights on navigating costs, pricing strategy, and operational shifts. Designed for fast-moving leaders who want clarity, not complexity.
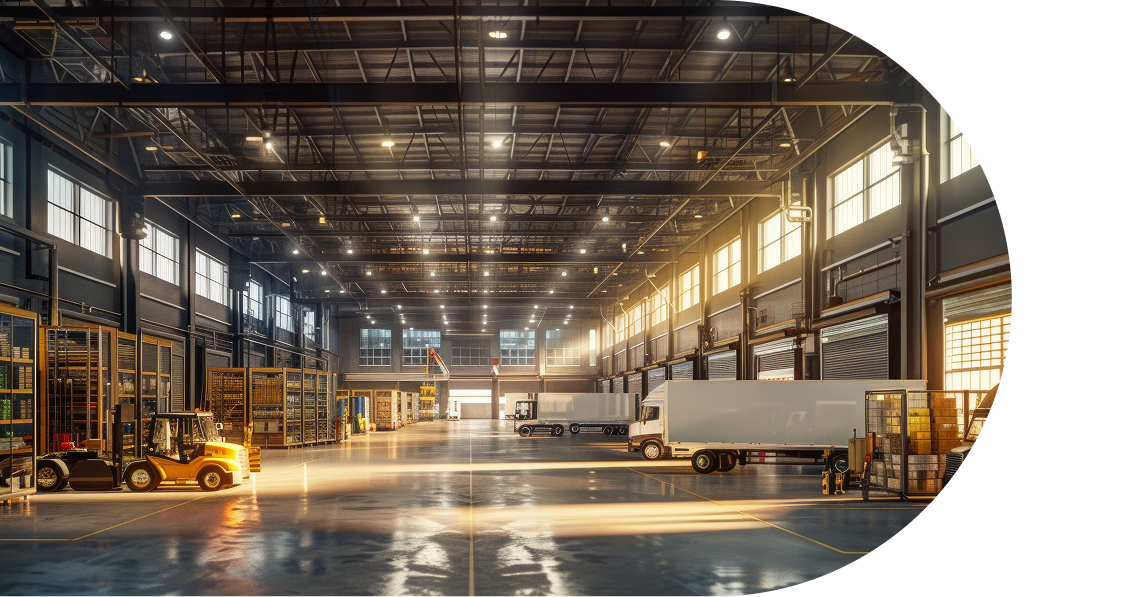
What are you leaving on the table?
In 30 minutes, our Growth & Margin Snapshot will show you where you’re losing margin, momentum, or missing opportunities—and what we’d do about it. Let’s talk.